We are now ready, after comprehensive in place testing, to unveil and launch our exclusive Dicom Connect client platform to all our customers new and old (if their existing Dicom equipment is fitted with RMS and they would like to upgrade the equipment as an optional extra). This system links to our already proven Remote Monitoring System (RMS). It is crucial that you can make quicker and more informed cost-effective decisions regarding your business operation and make the most of your investment in equipment. Here at Kadant PAAL we understand this and can make the changes you need to operate your compaction and baling equipment effectively. One of the many benefits of having the Dicom Connect on compaction equipment at source is that it will communicate directly with the client’s waste management services. This becomes efficient and effective practice on both sides in terms of transport only being despatched for full load collections and less charges being made to the source for part loads being collected, Sustainability being increased, and environmental impact being reduced.
We have been operating our RMS since Q1 2016 which has been very popular with our clients. For those not already aware the RMS allows Kadant PAAL to dial into our client’s machinery for diagnostics and managing factory settings to suit individual operational needs. This gives our clients a huge advantage of being able to diagnose and solve any issues by communicating directly with the machine user. Benefits being lower service call out costs and also massively reducing downtime by identifying parts required and enabling our Field Service Engineer to attend site fully equipped if required.
Dicom Connect is the client platform where operators can navigate a dashboard to use key features to produce operational information for management and operational performance within their facility.
This system is available for our range of Dicom Static Compactors, Dicom Portable Compactors and Dicom Vertical Balers allowing high level data to be produced and used within the organisation for optimal performance. Data collection will allow you to follow your waste management performance, enabling you to compare historical with live performance and have a location and status overview. All these factors ensuring you create an efficient, cost-effective facility.
Features such as live performance status, multiple device type access, managing user groups and notification subjects are a few examples of how Dicom Connect will be an asset to your operation. By choosing our product you will be able to access valuable data to maximise your waste management operation.
P.H.Hull & Sons Recycling Services have played an integral part in the initial testing of the Dicom Connect product. Initially with stringent and comprehensive testing of three Dicom Connect systems supplied for different compaction equipment, P.H.Hull & Sons put the system through its paces. Proof of the pudding is that now to date they have 12 installed Dicom Connect sytems on compaction equipment that processes different materials such as food waste i.e vegetable, bread, Category 3 waste and general waste. They regularly share performance read outs from the equipment enabling them to show the high performance they can achieve with this monitoring, reaping benefits for the client and the recycling services alike.
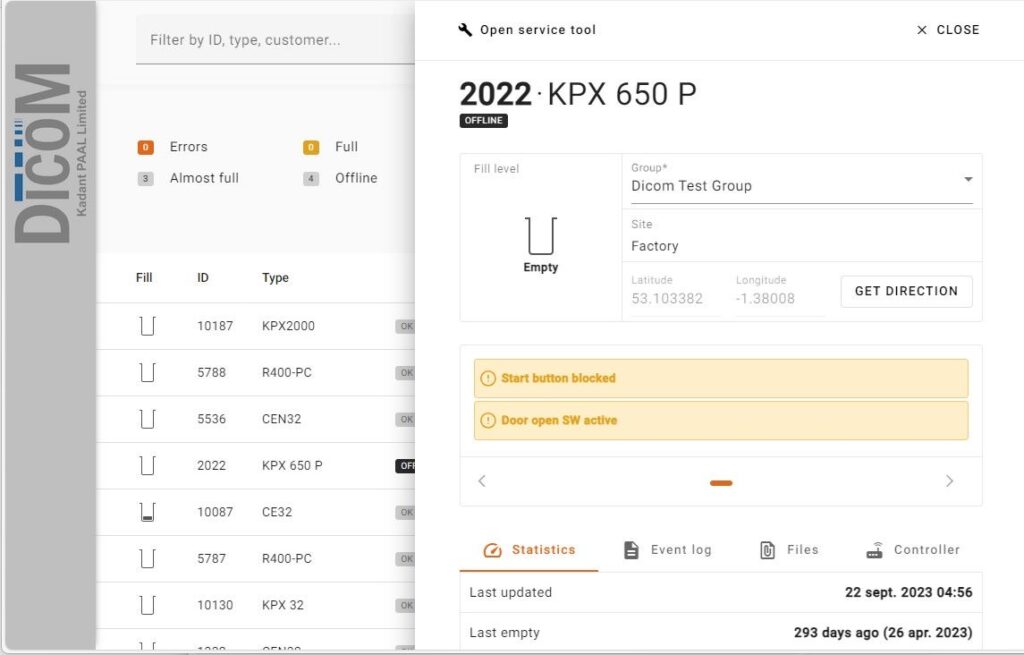
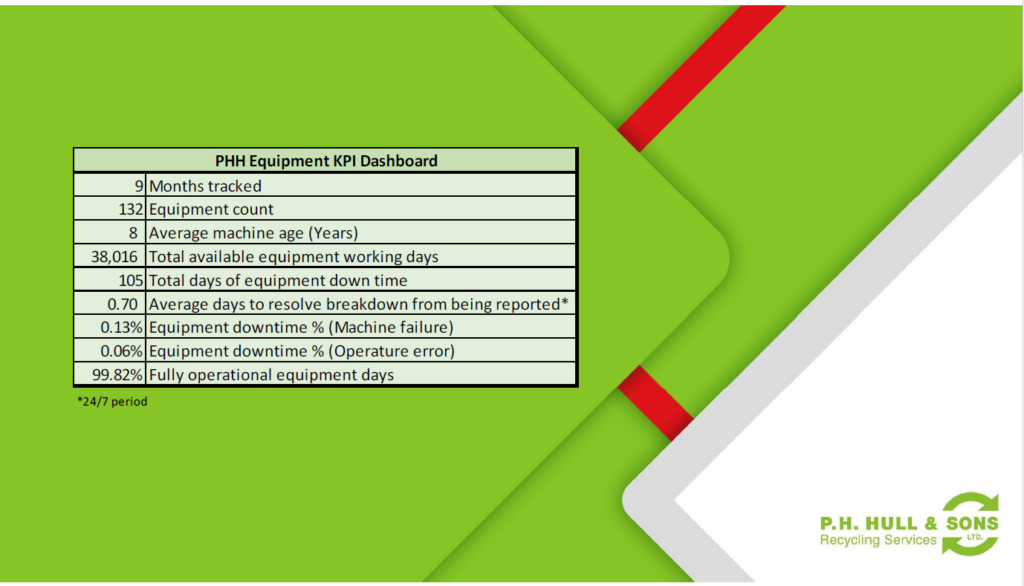
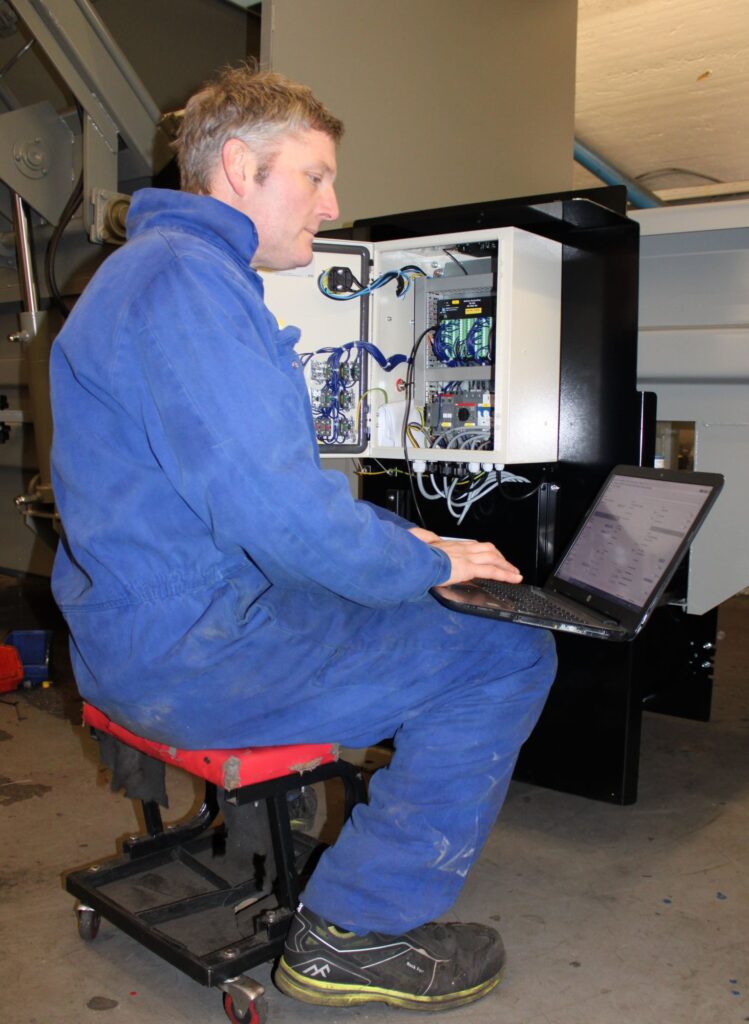
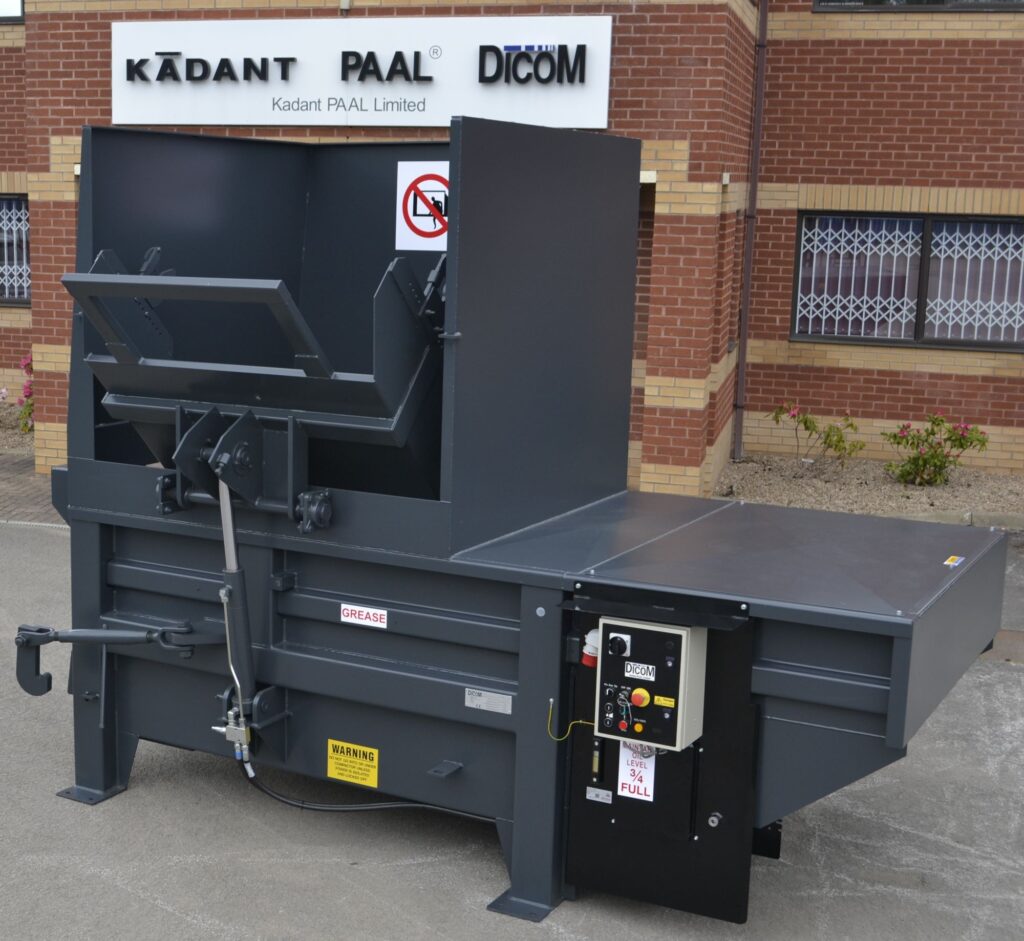